Building a car from the ground up is very difficult, and requires many people with many types of skills. Additionally, engines are almost prohibitively expensive to design, so you may want to use a crate engine to power your custom vehicle.
Constructing the Body
The body is likely the easiest part of the vehicle to build, or you could simply choose to not make a bodied vehicle. It can be done as an entire body shell like the Wikispeed C3, or in many sections so if one of the sections is damaged, you don't have to replace the entire body or remove the entire body to repair it. An easy material to work with to build a body is fiberglass, though carbon fiber may be used instead if baking the results can be achieved. Metals can also be worked and cut into shape, but it would be quite difficult to build a one-piece body that way.
When designing your car, you will need to consider where the body will mount to the chassis so that it can withstand the aerodynamic stress it will be put through.
Building the Chassis
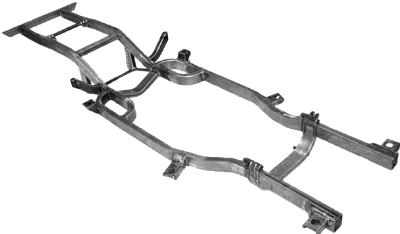
If you intend to sell a car like this, it is best to start with a chassis from another car, because most countries have laws which would require testing, which would mean you would have to build multiple copies of the car you wish to sell. Using a chassis from an old sporty car is popular because they are lightweight, somewhat bare, and usually have room to make unusual body shapes or additional chassis components.
If you aren't in a situation that would require that limitation, most from-scratch cars (especially top-tier racing vehicles) are constructed with metal tube frames. Metal tubes are relatively easy to work with and often produce better results than mass-produced cars.
When designing the chassis, many factors must be considered, including your specific needs, but almost every attempt with have to consider the following:
- Suspension Type & Geometry
- Driver, Engine, & Storage Space
- Structural Rigidity
- Intended Body Shape
- Overall Size & Weight
- Safety Component Locations
- Intended Ride Height
- Cooling Air Flow Points
- Wiring, Sensors, & Lighting
- Drivetrain & Steering Component Mounting Points
Making the Engine
Building an engine is possible, but very difficult without the proper machinery, engineering, and metal. A lot of metal must be used to cast the block, which will have various points drilled or milled out, such as the cylinders and valve guide mounting points. Channels for both coolant and oil must also be considered. Many bolt holes must be drilled out and tapped so that removeable outer parts such as valve covers or the oil pan can be attached, and those surfaces must be machined smooth so that their respective gaskets can properly seal.
Custom-design engine blocks can be made out of a large billet of metal to make almost any design, but parts like pistons and a crankshaft will also have to be made to match the specifications of the block, which means any repair items will also need to be manufactured this way. An engine block may be designed with off-the-shelf parts in mind to reduce costs and production time.
A Cylinder Head Being CNC Machined
Billet Engine Blocks
The closest the typical person can get to making their own engine from scratch is making one on a 5-axis machine from a piece of billet metal. Just renting the facilities to do this job is likely the most expensive part of an entire from-the-ground-up vehicle build project.
Most manufacturers of limited production run cars tend to use an engine from another manufacturer. Manufacturing well-built engines is a difficult task and going with a high-production-count engine means replacement parts are more readily available.
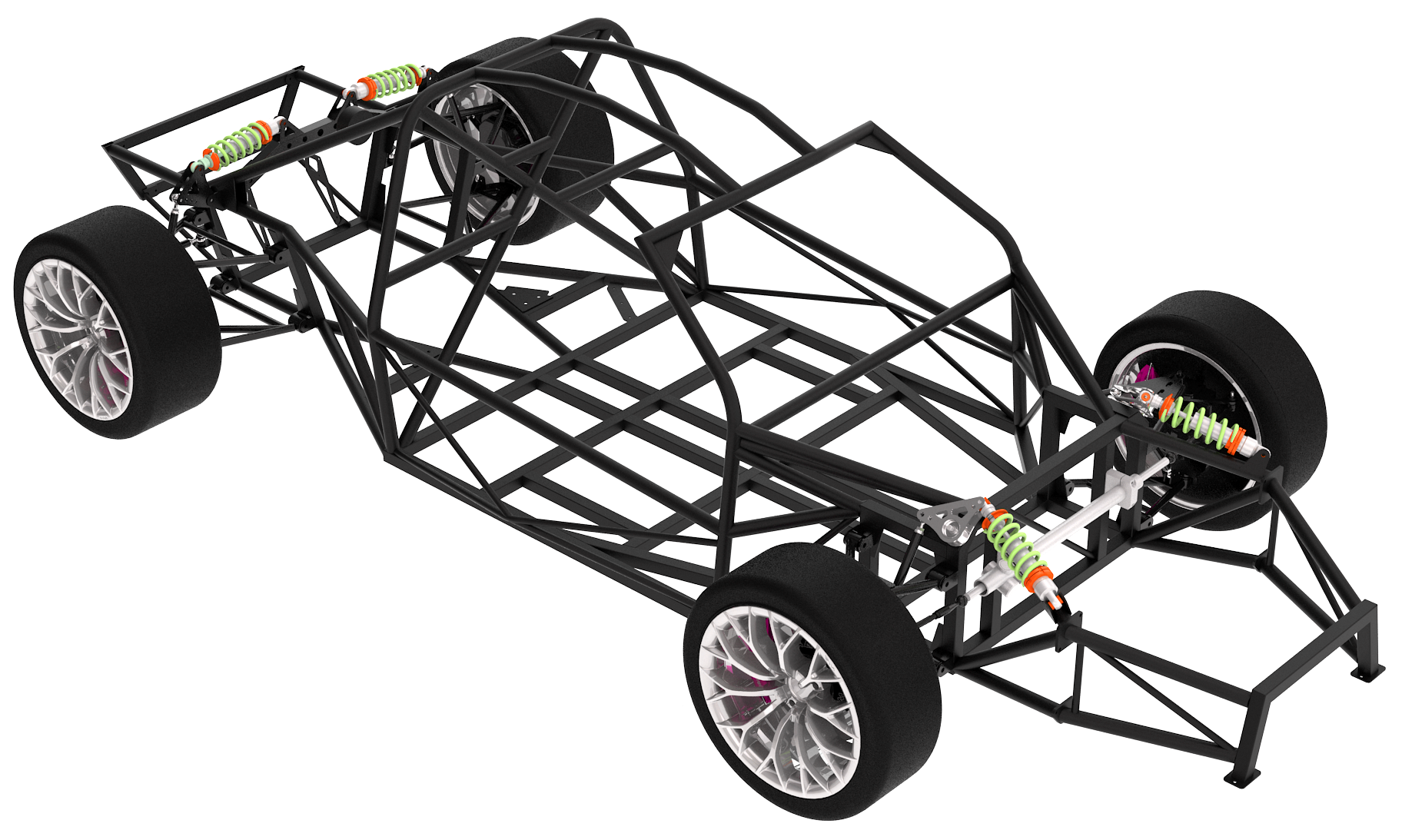